Projects
This section highlights the projects that I have worked on since starting graduate school. The overarching theme of the projects is designing energy efficient mechanisms; I work on heat switches, soft robots, and jumping mechanisms. My undergraduate projects can be found here.
Completed Projects
Mechanical Radiative Switch
Overview: Currently (2023), about 50% of US building energy consumption goes towards heating and cooling buildings. While climate change will increase the need for cooling, heating needs will remain high and even increase in some areas. In addition to using better insulation and appliances to save energy, harnessing the Sun and deep space for passive radiative heating and cooling, respectively, provides another means for reducing energy consumption.
While solar heating is rather straightforward, radiative cooling is less obvious. The atmosphere transmits and absorbs certain wavelengths of light. Most visibly, it transmits visible light well. Less visibly, it transmit infrared light between 7-14 μm well too. Coincidentally, most objects on Earth's surface emits most intensely at around 10 μm. This means a large fraction of our emitted infrared light goes directly into space. This allows us to passively cool things to below ambient temperatures. Some groups even achieve sub-ambient cooling in direct sunlight.
Prior to our work, other groups built devices that switch between solar heating and radiative cooling states, but they either used active switching mechanisms, had poor spectral property changes, or needed a large temperature range to switch states.
To achieve high passive performance, we used a wax actuated louver design. When the tiles are cold, the wax is frozen and in a low volume state, which pulls the louvers closed. This exposes a black colored low infrared emittance-high solar absorbance material to the sky. During the day, this results in efficient solar heating and during the night it minimizes infrared losses. When the tiles are hot, the wax is liquid and in a high volume state, which pushes the louvers open. This exposes a white colored high infrared emittance-low solar absorbance material to the sky. During the day, this reduces solar heating and at night maximizes infrared losses.
For our actuator, we modified a wax motor from a lawn mower and filled it with hexadecane which melts at 18.2°C (64.8°F). For our black colored material, we used black chrome and for our white we used a barium sulfate based paint. We made the rest of the tile with a mix of machined aluminum parts and 3D printed plastic parts.
For testing, we compared three devices: 1 fixed in the white state, 1 fixed in the black state, and 1 active. We measured the equilibrium temperature of the tiles and the heat flux required to maintain the underside of the tile with 1.5°C of 18.2°C.
Contribution: I did the prototyping, experiments, modeling, and most of the writing.
Results:
-
We built a tile-like radiative switch that passively switches between cooling and heating states
-
It switches between cooling and heating states within 3°C of the switch temperature
-
Compared with static devices, it reduces cooling and heating needs by more than 2.5×

![]() |
---|
![]() |
Light- and Heat-Seeking Vine Robot
Overview: Vine robots are robots made of an inverted, flexible, thin-walled pneumatic tube that everts when pressurized, lengthening from its tip. Like vines, they "grow" into their environments rather than move through it. Because there is no relative motion for the growth process, these robots readily move through constrained environments. Actuators along the sides of the vine robot control the pose of the robot.
Prior to our work, the control of these actuators and the processing of sensor data was centralized. Signals were transmitted and received via wires, cables, and pneumatic lines running down the center of the vine robot. This approach made vine robots with high degrees of freedom impractical.
To overcome this limitation, we propose a "materials-level" approach so that the robot responds to stimuli at the local level. To achieve this, we use a series of pouches filled with low boiling point fluid and light absorbing fabric. We call these actuators Photothermal Phase-change Series Actuators (PPSAs). When these pouches heat up, they inflate radially and contract in length, which can result in local bending. The greater the heating, the greater the contraction.
In the paper, we characterized the behavior of PPSAs and demonstrated vine robots that can find heat and light sources autonomously.
We envision using similar robots for fighting smoldering fires.
Contribution: I contributed to the experimental design, testing, modeling, and writing.
Results:
-
Development and characterization of PPSAs.
-
Characterization of vine robots that use PPSAs.
-
Demonstrated that these robots can autonomously find heat and light sources.
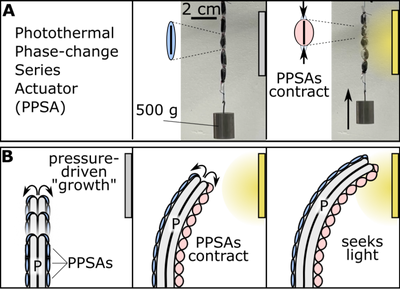
Thermal Fluctuation Energy Harvesting
Overview: Temperatures often change over time. On Earth, we typically experience this as the diurnal temperature cycle. We can extract energy from this thermal variation.
One way to extract this energy is to use low boiling point fluids. Temperature changes result in vapor pressure changes, making it possible to do work. Some clocks, most notably the Atmos clocks, use this method to wind their movements.
Inspired by the clocks, we propose using this method to power robots in remote areas. To improve performance, we made two modifications. The first of the modifications is using a constant force return spring. This allows for more useful work per stroke. The second modification is using a fluid that when under ambient pressures boils below the operating temperatures. We then "tune" the boiling point by using a constant force spring to preload the actuator. Doing this provides two advantages. The first of which is that at allow us to use more working fluids. The second of which is that the vapor pressure-temperature relationship is nearly exponential. This means that fluids with lower boiling points usually have larger pressure differences for the same temperature range than fluids with with higher boiling points, allowing for more work per stroke.
Note that maximizing work per stroke does not guarantee greater thermodynamic efficiency; however, often, in the proposed application the number of cycles is the limiting factor rather than the available heat. Therefore, one needs to maximize work per stroke.
To test this approach, we built a rolling diaphragm like actuator filled with butane. A constant force spring tuned the boiling point. For a demonstration, we built a small wheeled vehicle that moved about 10 meters after 1 stroke.
Contribution: I did the prototyping, experiments, and most of the writing.
Results:
-
Built and tested an actuator that harvests energy from thermal fluctuations.
-
Demonstrated that the energy harvesting actuator can power a small vehicle 10 meters.
High Jumping Jumpers
Overview: Jumping is an intriguing problem. It is simple yet full of subtlety. Why do animals jump the heights they jump? How do we build things that jump high? For centuries, scientists have studied the physics of jumping in biology, and for decades, engineers have built biologically inspired jumpers. Despite the intense study, little work has been done to compare the scaling laws of biological and engineered jumpers.
In our work, we show that engineered systems can jump much higher than biological ones because they can store significantly more energy in springs. Biological motors can only do a single stroke, which limits the amount of work they can do. In contrast, rotary motors and ratchet mechanisms allow engineered systems to do work over and over again. It allows for "work multiplication."
Using this insight, we built a jumper that can jump over 30 meters high. To do this, we maximized the spring to motor ratio and used a novel carbon bow-latex composite spring. Latex has a high specific energy and we used it to reduce the peak bending stress in the carbon bow springs and store more energy.
Results:
-
Explained that the difference in achievable jump heights between biological and engineered jumpers comes from work multiplication.
-
Developed a new a carbon bow-latex spring that allows for high energy storage density.
-
Built a jumper that jumps over 30 meters high.
Contribution: I primarily contributed to the modeling in the paper.
Miscellaneous: The history of the project is interesting and detailed here.
In Progress
Increasing Soft Heat Engine Efficiency
Overview: Liquid to gas phase change is an attractive way to inflate soft robotic actuators, because it eliminates the need for bulky pneumatic lines and compressors; however, it is inefficient (<<1%). By developing strategies that increase efficiency, we can make soft robots more agile and practical.
Jumping Even Higher
Overview: Our previous work explained how engineered jumpers jump higher than biological ones; however, it does not fully explain how to optimize jumper design. We are taking a closer look at the physics of jumping and have found new design insights.
Jumping on the Moon
Overview: The rocky terrain of the Moon and the lack of atmosphere makes jumping an attractive mode of locomotion. We have been testing technologies related to jump energy recovery and controlling the jump direction.